Extend the Life of Your Product Packaging Devices With Specialist Repair Work
In today's affordable landscape, the long life and efficiency of packaging devices are paramount for keeping functional quality. Engaging professional repair work services not only addresses instant mechanical and electric concerns yet additionally cultivates a society of regular upkeep that can considerably improve devices performance. With proficient technicians geared up to utilize top notch components that line up with maker requirements, organizations can mitigate downtime and lower functional prices. Nonetheless, recognizing the full scope of benefits and the appropriate strategy to choosing a repair work solution can be crucial, bring about a much more strategic financial investment in your equipment. What should business think about next?
Value of Regular Upkeep
In the realm of product packaging equipment, the importance of regular upkeep can not be overemphasized. Routine upkeep ensures that machinery operates effectively, reducing the chance of unexpected break downs that can interfere with production timetables. Regular maintenance entails systematic assessments, cleansing, lubrication, and adjustments that are crucial for ideal efficiency.
Moreover, maintenance works as a proactive technique to recognizing prospective problems prior to they rise into costly repair services. By resolving minor deterioration immediately, organizations can extend the life expectancy of their devices, safeguarding their capital expense. This precautionary approach not only reduces downtime however likewise boosts overall productivity.
Furthermore, normal upkeep plays an important function in ensuring compliance with security criteria and policies. Properly maintained machinery is less likely to present safety dangers to drivers, thereby promoting a much safer working atmosphere. It likewise helps in preserving item top quality, as effectively operating devices is essential in sticking to specifications and minimizing defects during the packaging process.
Benefits of Expert Repair Work

Moreover, professional fixing services commonly use high-grade components and products that fulfill or go beyond maker specs. This dedication to high quality guarantees that the repaired equipment operates at optimal performance degrees, extending its life expectancy and minimizing the probability of future breakdowns.
Furthermore, expert repair work can result in cost financial savings over time (packaging machine repair). By dealing with issues quickly and effectively, businesses can avoid the high costs connected with complete equipment replacements. Regular specialist upkeep can enhance the performance of packaging equipments, leading to increased productivity and, subsequently, greater success.
Lastly, counting on professionals for repair work cultivates conformity with market criteria and safety laws, mitigating dangers connected with inappropriate handling of equipment. Essentially, spending in expert fixing services not just receives equipment performance but likewise adds to a more effective, secure, and profitable functional setting.
Common Packaging Tools Issues
Understanding typical product packaging equipment problems is vital for preserving functional efficiency. Product packaging equipment usually faces a variety of troubles that can interfere with production and compromise product stability. One widespread concern is mechanical failure, which can stem from worn-out elements, imbalance, or absence of lubrication. Such failings might lead to unexpected downtime and expensive fixings (packaging machine repair).
An additional usual concern is electric breakdowns. These can result from defective electrical wiring, blown merges, or out-of-date control systems. Electric issues can trigger equipment to operate erratically or fail to begin completely, affecting the entire packaging line.
Additionally, product jams frequently occur due to official site improper configuration, debris accumulation, or used components. Jams not just halt production but might also damage the items being refined, bring about more losses.
Moreover, inconsistent sealing or labeling can emerge from tools wear or wrong calibration, weakening product quality and compliance with sector criteria. Last but not least, poor upkeep practices frequently contribute to a decrease in devices performance, making regular evaluations and servicing necessary. By identifying and dealing with these usual problems, firms can enhance their product packaging operations and extend the life-span of their devices.
Picking the Right Repair Service Solution
Choosing the appropriate repair solution for product packaging equipment is critical to reducing downtime and making certain operational effectiveness. When evaluating possible company, consider their proficiency and field of expertise in the kind of devices you make use of. A company with a tested track document in your details machinery will likely use even more reliable and reliable repair work.
Furthermore, analyze the qualifications and accreditations of the professionals. Experienced experts that are skilled in sector criteria can identify issues faster and implement services better. Researching client evaluations and testimonies can likewise provide insight into the provider's reputation and see this site dependability.
Another essential element is the availability of emergency support. Tools failings can happen suddenly, and having access to a responsive repair service can significantly reduce the influence of downtime. Moreover, make inquiries concerning the service warranty used on repair services, as this can show the self-confidence the company has in their job.
Last but not least, think about the communication and assistance framework of the repair service. A business that focuses on customer care will certainly not only maintain you notified throughout the repair work process yet will additionally be a lot more likely to supply continuous maintenance referrals to prolong the life of your devices.
Price Financial Savings Via Expert Repair Services
How can purchasing specialist repair work lead to significant expense financial savings for your packaging devices? Involving experienced service technicians for repairs guarantees that concerns are properly diagnosed and efficiently attended to, preventing further damage and expensive downtime. Specialist repair services use specialized understanding and devices, which can bring about extra efficient maintenance than in-house efforts, as a result minimizing labor prices.
In addition, prompt repairs can extend the lifespan of your equipment, delaying the need for expensive substitutes. By maintaining optimal functioning, you also enhance production efficiency, which translates to lower operational prices. When devices run smoothly, there is less waste, and efficiency degrees stay high, permitting for far better earnings margins.
In addition, professional repair work typically feature assurances or guarantees, giving assurance and economic security against future failures. This guarantee can alleviate unexpected expenses and promote far better budgeting for maintenance.
Lastly, buying expert repair solutions promotes a proactive strategy to devices management, advertising a culture of normal maintenance checks. This strategy better improves overall devices reliability, inevitably causing sustained price savings over time. Prioritizing specialist repair services is thus a smart financial choice for companies reliant on product packaging equipment.
Verdict
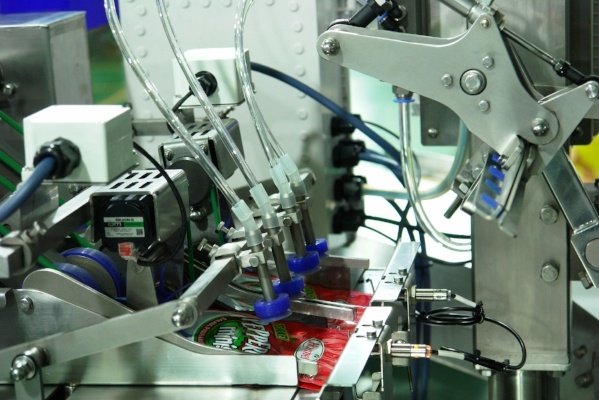
Engaging specialist repair service services not just addresses immediate mechanical and electric issues however also promotes a society of routine upkeep that can substantially improve tools efficiency.Professional repair service of product packaging devices supplies various advantages that can dramatically improve operational performance.How can spending in specialist repair work lead to considerable price savings for your product packaging equipment? Prioritizing expert fixings is thus an intelligent monetary choice for businesses reliant on packaging tools.
In verdict, the longevity and effectiveness of product packaging tools can be significantly improved with normal upkeep and professional repair work services.
Comments on “The Importance of Timely Packaging Machine Repair for Your Business”